Process Improvement - www.ussteel.com
INSPIRING INNOVATION
Process Improvements
At U. S. Steel, our mission of delivering profitable steel solutions for people and planet underlies everything we do. In 2023, supported by our Board of Directors (Board), we continued our work to fulfill this mission by executing our strategy to deliver the BEST for all our stakeholders. Along with adding mini mills to our arsenal, we are focused on improving the capabilities of all our operating sites to ensure we can produce as many of our products as possible by both the integrated and mini mill processes. These efforts will help us as we continue to work toward our goal to achieve net-zero Scope 1 and 2 GHG emissions by 2050. Our deep understanding of metallurgy and processing technology paired with more than a century of understanding our customers’ needs is the key to creating highly specialized products.
We are also incorporating proprietary automated analytics tools and monitoring systems to optimize our products and systems. Advanced analytics have helped us assess product lifespans, improve our emergency response and reduce our carbon emissions, supporting values across our S.T.E.E.L. Principles.
We have undertaken a variety of advanced process improvement projects:
Keetac DR-Grade pellets
This project represents a $150 million investment in direct-reduced-grade (DR-grade) pellet capabilities at our Minnesota Ore Operations Keetac taconite plant in Keewatin, Minnesota. DR-grade pellets supply a key input for the feedstocks used in lower-emissions electric arc furnaces (EAFs), improving their quality and efficiency. Keetac will gain the flexibility to supply pellets for our existing blast furnaces and EAFs. The project was completed in late 2023, with the first pellets produced in 2024.
metriX
Implemented at the plant level, metriX is the next evolution of continuous improvement. It tracks progress on cost-savings, sustainability-related improvement projects on a monthly basis. This program is modeled after the Define, Measure, Analyze, Improve, Control (DMAIC) process:
+ Define the issue, opportunity for improvement, and improvement goals and activities
+ Measure and track performance
+ Analyze the progress to determine any weaknesses in the process
+ Improve performance by determining root cause of any weaknesses
+ Control the improved process and future performance
In 2023, we made significant improvements to our processes utilizing metriX.
More information on our continuous improvement projects can be found in Protecting our Planet.
Gary Works Forms Digitization:
As a first step in a broader effort to digitize and streamline a range of processes at our Gary Works, the plant has digitized several medical and safety forms and made them available on mobile devices. The project is saving the time and paper required to manually print, distribute, process and track paper forms, increasing productivity and facilitating faster responses to employee needs. A number of other processes are scheduled for digitization in 2024.
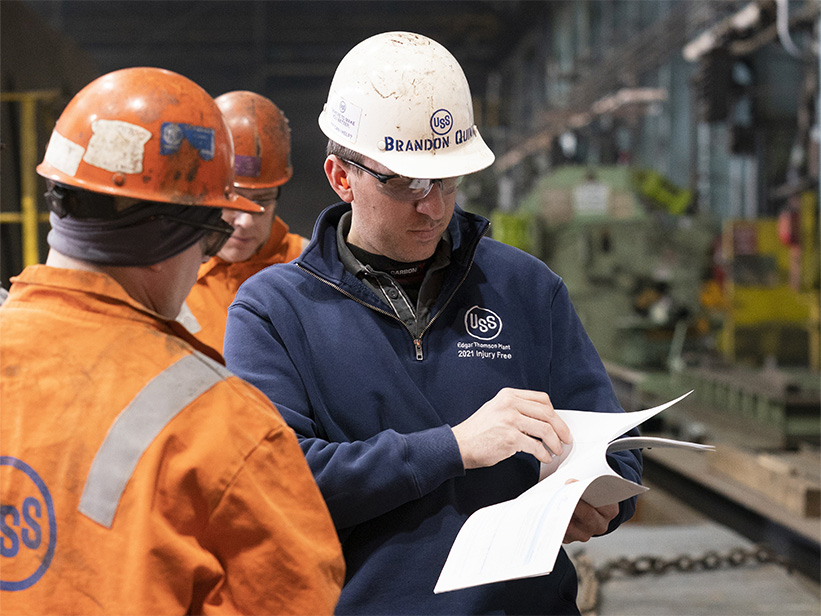
MineMindTM, developed using Google Cloud
An AI-driven application that aims to simplify equipment maintenance by providing optimal solutions for mechanical problems, saving time and money, and improving productivity. MineMind™ reduces the amount of time needed to complete a work order by an estimated 20%. The initial phase of the launch began in August 2023, with the installation of a foundation AI technology platform owned, operated, and secured by U. S. Steel's IT team. Google Cloud and U. S. Steel worked together to deploy MineMind as a production-ready app that began preliminary testing in April 2023. We are excited that our maintenance teams at Minnesota Ore Operations (Minntac and Keetac) will have the ability to harness the power of Google Cloud’s generative AI technology as a secure app, running alongside their existing technology and solutions. The application will impact more than 60 haul trucks at U. S. Steel's Minnesota Ore Operations Minntac and Keetac facilities.
Pig iron caster at Gary Works
This investment in Gary Works is creating needed material for our lower-emissions electric arc furnaces, combining the best of integrated and mini mill technologies. The pig machine will be fed with iron ore from the Company’s Minnesota Ore Operations, Minntac and Keetac. The produced pig iron is expected to supply up to half of the ore-based metallics needs for U. S. Steel's Big River Steel Works.
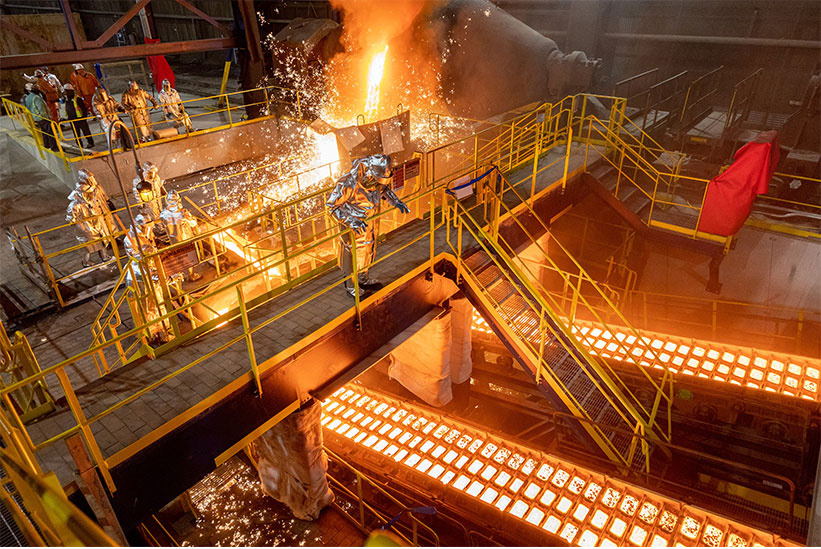
Automated thread gaging systems at the Offshore Operations Houston facility
The tubular plant deployed two automated, non-contact premium thread gaging systems at the Offshore Operations Houston facility in Houston, Texas. The automated systems were designed to replace less precise manual mechanical gaging methods that have been used for several decades. Additionally, they eliminated an inspection bottleneck, increasing overall productivity of the threading line by 40% and delivering $1.34 million in cost savings in 2023.