Sustainability - Environmental - Waste Management, Recycling & Reuse - www.ussteel.com
Environment
Waste Management,
Recycling and Reuse
Steel is the most recycled material in the world, but that’s not the only thing we recycle and reuse from our operations.
Every year, U. S. Steel recycles substantial quantities of scrap metal and other steelmaking coproducts and byproducts.
Steel has always been infinitely recyclable, and U. S. Steel's history of recycling is long. The products made with steel help contribute toward a circular economy. Because of steel’s physical properties, steel products can be recycled at the end of their useful life without loss of quality. The ability to recycle steel also contributes to its affordability.
Recyclability rates in the
United States
Steel
90%
aluminum
<75%
Paper
<70%
Glass
33%
Plastic
10%
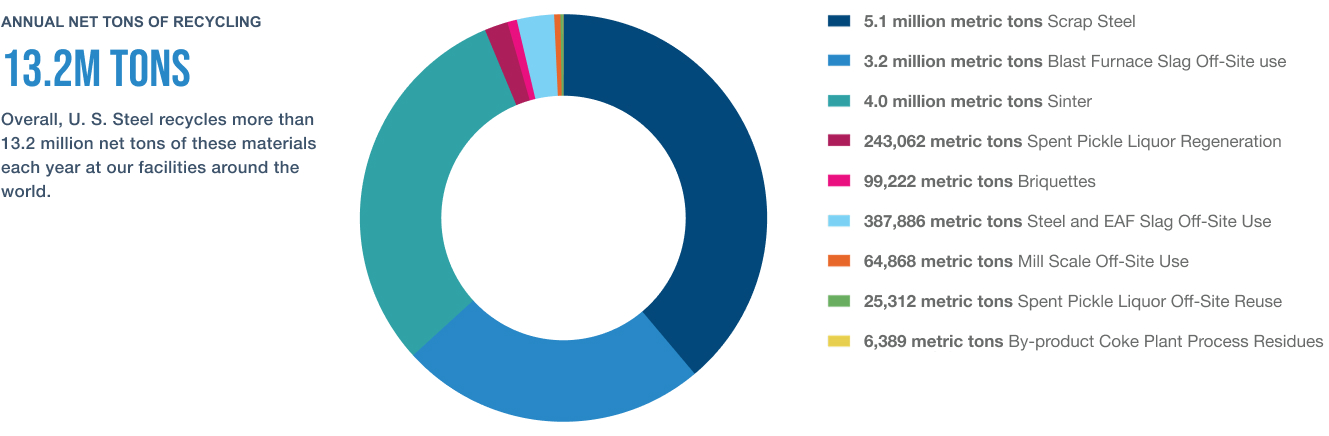
U. S. Steel’s waste management, recycling and reuse efforts focus on the following areas:
In 2024, U. S. Steel recycled approximately 3.2 million metric tons of blast furnace slag and 284,080 metric tons of steel slag. Blast furnace (iron) slag and basic oxygen furnace (steel) slag are highly sustainable products that are used in place of natural aggregates, such as limestone and gravel, in numerous construction and product applications. Blast furnace slag is used in cement manufacturing, asphalt mixes, glass manufacturing, precast concrete, wallboard, mineral wool, and sub-base for road and interstate highway construction. Steel slag, which like blast furnace slag can be used in cement manufacturing and asphalt mixes, is also recycled in applications such as landfill daily cover and internal haul roads, phosphorus removal in wastewater treatment, ground water remediation, reactive barrier walls, and agricultural applications, including as a liming agent and micronutrient in fertilizer. Use of iron and steel slag in place of mined and quarried rock and mineral aggregates saves these natural resources and reduces the impact to the environment.
U. S. Steel also works with outside organizations to repurpose our used equipment. Examples include transforming used conveyor belts into rubber mats and used tires from our mining mobile equipment into feeding and water troughs for livestock. At USSK, construction waste, like concrete, debris, and ceramics from reconstruction and modernization projects, is reused by third parties, a recycling effort that has continuously minimized the use of landfills.
We reduce the amount of waste generated and emissions produced in steelmaking by reusing the byproduct gases produced in our blast furnaces and coke ovens because it is good for the environment and good for business.
U. S. Steel Mon Valley Works is one of the most energy-efficient integrated iron and steel facilities in the world. The Mon Valley Works reuses gases from blast furnaces and coke ovens to support combustion processes at U. S. Steel’s Clairton, Edgar Thomson, and Irvin facilities, as well as to generate electricity at the Edgar Thomson and Clairton plants. The Mon Valley Works is a certified Alternative Energy System recognized by the Pennsylvania Department of Environmental Protection (PADEP).
We optimize energy use by capturing and repurposing excess coke oven gas (COG) generated at our Clairton facility. This recovered gas is distributed through a dedicated pipeline to our Irvin and Edgar Thomson plants, where it serves as a cleaner-burning fuel source. On average, we redirect 80–90 million cubic feet of COG per day—enough energy to heat approximately 44,000 homes— maximizing energy efficiency through resource recovery.
At our Minnesota Ore Operations in the Mesabi Iron Range, we operate several highly efficient taconite mines—Keetac and Minntac. The stockpiling of materials not suitable for processing is regulated by the Minnesota Department of Natural Resources (MNDNR). Waste rock and surface material must be removed to uncover the taconite that will be processed. Waste rock and surface overburden are stockpiled around the active mining area and around previously mined areas. U. S. Steel complies with MNDNR design and construction standards for stockpiles, as well as reclamation standards. Annual reports are sent to MNDNR that address both completed and planned reclamation activities. Approximately 70% of the processed taconite is non-iron-bearing materials that are generated as tailings. Minntac and Keetac both operate tailings basins for the storage of tailings that are approximately 8,000 and 6,000 acres, respectively. Each of the tailings basins features active interior tailings disposal basins (6,000 acres and 2,400 acres, respectively) with separate exterior perimeter dams. They utilize an instrumentation network around the tailings impoundment to routinely monitor the dam. Routine inspections are performed at both facilities, including observing for damage. Inspections are performed by knowledgeable personnel or third-party engineers. Inactive areas of the tailings basins are reclaimed. Dam safety reports that review the annual activities and monitoring are provided to MNDNR annually. MNDNR also conducts independent inspections of reclamation success and dam safety.
U. S. Steel recycles several other materials from the byproduct, cokemaking, ironmaking, steelmaking, and steel finishing operations. In 2024, 6,389 metric tons of process materials from the cokemaking byproducts plant were collected and returned directly to coke ovens. Carbon, iron, and steel bearing residuals, such as coal and coke fines, taconite pellet fines, blast furnace and steel furnace air pollution control dusts and sludges are used to produce sinter and briquettes, which are then used as feedstocks for iron-making and steelmaking, respectively. This included the production of approximately 4.0 million metric tons of sinter, which was used in the blast furnaces, along with 99,200 metric tons of briquettes that was used in the blast furnaces and Basic Oxygen Process (BOP) furnaces.
An additional 64,868 metric tons of mill scale not used internally to make sinter or briquettes was sold to cement manufacturers, which use the mill scale for its iron content, a critical ingredient in cement. Hydrochloric acid, which is used in steel pickling operations to remove heavy iron oxide rust from the surface of steel coils to prepare the coils for surface coating, results in an iron oxide rich material called spent pickle liquor. The spent pickle liquor is recycled by being sent to a recycling plant to regenerate the hydrochloric acid and return it to plants for reuse in pickling, or it is sold for beneficial use as a wastewater treatment chemical.
In 2024, U. S. Steel reused 243,062 metric tons of regenerated hydrochloric acid in the pickling lines and sent 25,312 metric tons off-site for direct beneficial use in wastewater treatment.
In 2024, U. S. Steel recycled approximately 5.1 million metric tons of scrap steel in our integrated and mini mills. Steel can be recycled over and over without any loss of quality to the products being produced.
Environmental Areas of Focus
U. S. Steel’s current environmental areas of focus align with the results of our ESG Materiality Assessment.