Sustainability - Roadmap to 2050 - www.ussteel.com
Roadmap to 2050
Our vision to achieve our net-zero greenhouse gas emissions goal.
The global climate crisis poses challenges that differ in nature and are far beyond the scope of those that our society has faced during the 20th century. In the pioneering spirit of its founders, U. S. Steel is tackling this challenge head-on, through an ambitious transition to its Best for All® strategy. U. S. Steel has been on the forefront of transformational change since its inception—and we enthusiastically continue to tackle the challenges of our times.
As part of this vision, U. S. Steel is intensifying efforts to become an industry leader in lower-carbon emission steel production methods. In April 2021, U. S. Steel announced an ambitious goal to achieve net-zero greenhouse gas (GHG) emissions by 2050. This builds upon our previously announced goal to reduce greenhouse gas emissions intensity by 20% by 2030, compared to a 2018 baseline. Meeting these goals will require partnering to find new business approaches and develop new technologies, as well as advocating for collaboration and support of governments, trade agencies, and other organizations.
This webpage outlines our current path to achieve these ambitious 2030 and 2050 GHG reduction goals. Our transition to Best for All® will provide flexibility to adapt our efforts towards achieving our goals while accommodating changes in technology and business approach in the coming decades.
Scope 1 emissions are primarily derived from the manufacturing of our products at all of our facilities.
Scope 2 emissions are primarily derived from purchased electricity for our sites.
We currently do not measure or disclose Scope 3 emissions but are in the process of working with our suppliers to develop the data and processes to have this information available in the future, focusing on the upstream Scope 3 categories.
Scope 1 and Scope 2 emission and emission intensity trends are shown in the table below, along with crude steel production.
Emission data includes sites where U. S. Steel has operational control for a given year, however, owned office space, standalone laboratories, and facilities where emissions are consistently at a de minims level are excluded. Non-controlled joint ventures (e.g., Big River Steel before 2021 and PRO-TEC Coating Company) and leased office space were not included in the annual data reported for 2020 and earlier years. Operational sites include integrated steelmaking facilities, EAF-based steelmaking facilities, mining operations, and standalone finishing operations. Our GHG emissions for 2021 will include Big River Steel, a LEED-certified mini mill which was acquired on January 15, 2021. Going forward, footprint changes may occur through mergers, acquisitions, divestments, discontinuing operations and/or organic growth, which will likely be a component of our efforts to meet our reduction targets.
As part of this vision, U. S. Steel is intensifying efforts to become an industry leader in lower-carbon emission steel production methods. In April 2021, U. S. Steel announced an ambitious goal to achieve net-zero greenhouse gas (GHG) emissions by 2050. This builds upon our previously announced goal to reduce greenhouse gas emissions intensity by 20% by 2030, compared to a 2018 baseline. Meeting these goals will require partnering to find new business approaches and develop new technologies, as well as advocating for collaboration and support of governments, trade agencies, and other organizations.
This webpage outlines our current path to achieve these ambitious 2030 and 2050 GHG reduction goals. Our transition to Best for All® will provide flexibility to adapt our efforts towards achieving our goals while accommodating changes in technology and business approach in the coming decades.
EMISSIONS COVERED
Scope 1 emissions are primarily derived from the manufacturing of our products at all of our facilities.
Scope 2 emissions are primarily derived from purchased electricity for our sites.
We currently do not measure or disclose Scope 3 emissions but are in the process of working with our suppliers to develop the data and processes to have this information available in the future, focusing on the upstream Scope 3 categories.
Scope 1 and Scope 2 emission and emission intensity trends are shown in the table below, along with crude steel production.
Recent Trends in Greenhouse Gas Emissions
MILLION METRIC TONNES | TONNES CO2e/TONNES CRUDE STEEL | ||||||
---|---|---|---|---|---|---|---|
Crude Steel | Scope 1 GHG Emissions | Scope 2 GHG Emissions | Total GHG Emissions | Scope 1 Emissions Intensity | Scope 2 Emissions Intensity | Total Emissions Intensity | |
2018 | 15.35 | 32.1 | 3.3 | 35.4 | 2.09 | 0.21 | 2.31 |
2019 | 13.89 | 29.9 | 3.2 | 33.1 | 2.15 | 0.23 | 2.38 |
2020 | 11.54 | 24.9 | 2.0 | 27.0 | 2.16 | 0.17 | 2.34 |
Emission data includes sites where U. S. Steel has operational control for a given year, however, owned office space, standalone laboratories, and facilities where emissions are consistently at a de minims level are excluded. Non-controlled joint ventures (e.g., Big River Steel before 2021 and PRO-TEC Coating Company) and leased office space were not included in the annual data reported for 2020 and earlier years. Operational sites include integrated steelmaking facilities, EAF-based steelmaking facilities, mining operations, and standalone finishing operations. Our GHG emissions for 2021 will include Big River Steel, a LEED-certified mini mill which was acquired on January 15, 2021. Going forward, footprint changes may occur through mergers, acquisitions, divestments, discontinuing operations and/or organic growth, which will likely be a component of our efforts to meet our reduction targets.
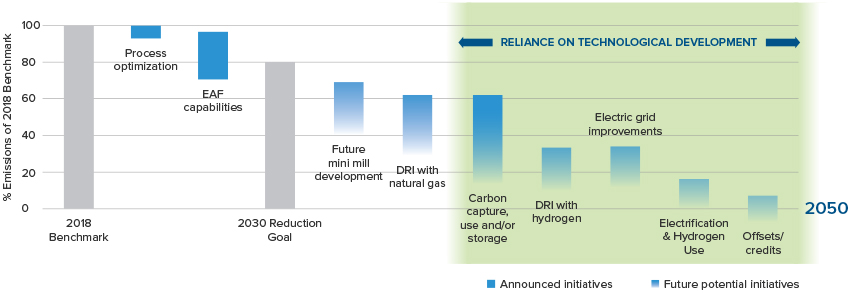
In November 2019, U. S. Steel announced our first greenhouse gas reduction goal of a 20% reduction in GHG intensity by 2030 from a 2018 baseline.
How will we get there?
Process optimization and clean energy procurement
For existing operations, we are continuously striving to use less energy, whether that energy is from purchased electricity, purchased natural gas, or the coal and coke used in our processes. We are working with our supplying utilities on improving access to carbon-free electricity, whether through direct investment, virtual power purchase agreements (VPPAs), or retiring credits. Depending on the availability of carbon-free energy, we anticipate that these efforts will result in a reduction of 3-6% in GHG emissions intensity. One example of this is our existing use of Renewable Energy Credits (RECs) at our Mon Valley Works and Granite City Works to ensure all of the electricity we purchase for those facilities is carbon-free.Integrating EAF capabilities into our footprint
Integrating EAF capabilities into our footprint is key to achieving our 2030 GHG goal. We have already made progress in this area with our acquisition of Big River Steel and completion of the construction of the Fairfield Works Tubular EAF, which resulted in approximately a 10-15% reduction in our GHG emissions intensity. We have announced the construction of a second mini mill (in Arkansas, near Big River Steel), which will further aid us in meeting our 2030 GHG goal. This second mini mill is expected to be operational in 2024, and with its incorporation of endless casting and rolling technology, we expect to further reduce GHG emissions intensity versus other thin slab casting technologies. Other examples of footprint changes include the permanent idling of our Great Lakes Works steelmaking and hot rolling operations. Additionally, we announced our intention to permanently idle Batteries 1-3 at our Clairton Coke Plant by March 31, 2023.
Taking the next step in our journey to reduce GHG emissions, in April 2021 we announced a bold ambition to achieve net-zero carbon emissions by 2050, making us the first North American steel company to announce such a goal.
Moving from our 2030 goal of a 20% reduction in GHG emissions based on intensity to our 2050 goal will involve the development of various technologies. This goal will entail additional EAF deployment and other developments in the industry. Due to the reliance on these future developments the exact timing, location, and final effect on U. S. Steel's emissions is currently uncertain and subject to change as developments occur. We have identified the following areas for potential emissions reductions and indicated those that require further development to become commercially feasible.
EAF technology, which currently exists and is widely used today, produces steel with approximately 70% less GHG emissions than traditional integrated steelmaking. To achieve net-zero emissions, U. S. Steel will further incorporate and utilize EAF-based/mini mill steelmaking technology in our footprint to achieve our 2050 net-zero goals. The level of improvement will depend on the number of mini mills deployed and could lead to reductions from 10-60% from the 2018 target.
Direct Reduced Iron/Hot Briquetted Iron (DRI/HBI) using natural gas
Iron ore is currently converted to iron for use in our blast furnaces using coke, a purified form of coal. As we increase our EAF-based steel production, we have the opportunity to utilize less carbon intensive raw materials in the production process. The adoption of DRI/HBI technology using natural gas as the reductant, to convert our iron ore into a product to be used by our growing fleet of EAFs will lead to increased efficiency and ability to incorporate more mini mills into our steelmaking, as well as reduce our reliance on coal and coke. The amount of reduction depends on how many DRI/HBI facilities are deployed but could range from 10-50% reduction from 2030. Natural gas based DRI has been used around the world for almost 50 years and is a mature technology.
Hydrogen-based DRI expands on work done earlier with natural gas-based DRI. Hydrogen-based DRI would replace the natural gas with up to 100% hydrogen. The hydrogen used would be generated from renewable energy, or so-called “green” hydrogen. Production of the volume of green hydrogen needed requires a significant build-out of the clean electricity grid, which is why we consider this a future potential technology. The reduction potential depends on the number of DRI facilities constructed, and whether those DRI facilities would start DRI production using natural gas (included in the section above) and subsequently convert to hydrogen DRI production or start up immediately using hydrogen for DRI production. Assuming natural gas based DRI is then converted to hydrogen, we would expect a further 20-40% reduction in greenhouse gas emissions. While this technology is generally known, it is not commercially available yet.
Carbon Capture, Use, and/or Storage
The introduction of Carbon Capture, Use, and/or Storage into our operations can lead to decreased emissions. We expect that operational blast furnaces will eventually need to have some sort of carbon capture technology employed to continue operating by mid-century. Carbon capture currently exists in the power industry, however there is limited experience in the steel industry, and we do not expect it to be fully commercialized for at least another decade, although there are a number of potential vendors developing the technology. This includes the potential of capturing carbon dioxide from our integrated operations (e.g., coke plants, blast furnaces, oxygen steelmaking furnaces) as well as exploring the potential to capture carbon from our EAF-based operations. The amount of reduction depends on the deployment and the future asset base and potential reductions are not estimable at this time.
Electric grid improvements
Electric grid improvements are needed to allow U. S. Steel to obtain reliable, low-cost, carbon-free power at all our operating locations. While we do procure some carbon-free power currently, we consider this accelerating after 2030 due to several factors including:
Expansion of electrification and hydrogen use
Throughout our processes, we use carbon-containing fuels such as natural gas, diesel, fuel oil, and/or gasoline for process heating, building heating, and transportation. We believe we will be able to reduce our use of these carbon-containing fuels by increasing our use of hydrogen and/or electricity, reducing GHG emissions. This includes using hydrogen or electricity to replace natural gas in hot strip mill reheat furnaces and annealing furnaces, as well as examining the potential for the use of either of these to power light-, medium- and heavy-duty mobile equipment.
Carbon offsets/credits
To achieve net-zero emissions by 2050, we anticipate any gaps remaining from the above processes can potentially be closed through the use of carbon offsets or credits. Offsets and credits are a last resort, and our preference would be to lower emissions as much as possible through technological means before purchasing offsets and credits.
Improvements based on existing technologies
EAF technology, which currently exists and is widely used today, produces steel with approximately 70% less GHG emissions than traditional integrated steelmaking. To achieve net-zero emissions, U. S. Steel will further incorporate and utilize EAF-based/mini mill steelmaking technology in our footprint to achieve our 2050 net-zero goals. The level of improvement will depend on the number of mini mills deployed and could lead to reductions from 10-60% from the 2018 target.
Direct Reduced Iron/Hot Briquetted Iron (DRI/HBI) using natural gas
Iron ore is currently converted to iron for use in our blast furnaces using coke, a purified form of coal. As we increase our EAF-based steel production, we have the opportunity to utilize less carbon intensive raw materials in the production process. The adoption of DRI/HBI technology using natural gas as the reductant, to convert our iron ore into a product to be used by our growing fleet of EAFs will lead to increased efficiency and ability to incorporate more mini mills into our steelmaking, as well as reduce our reliance on coal and coke. The amount of reduction depends on how many DRI/HBI facilities are deployed but could range from 10-50% reduction from 2030. Natural gas based DRI has been used around the world for almost 50 years and is a mature technology.
Improvements based on technologies that require further development
Hydrogen-based DRI expands on work done earlier with natural gas-based DRI. Hydrogen-based DRI would replace the natural gas with up to 100% hydrogen. The hydrogen used would be generated from renewable energy, or so-called “green” hydrogen. Production of the volume of green hydrogen needed requires a significant build-out of the clean electricity grid, which is why we consider this a future potential technology. The reduction potential depends on the number of DRI facilities constructed, and whether those DRI facilities would start DRI production using natural gas (included in the section above) and subsequently convert to hydrogen DRI production or start up immediately using hydrogen for DRI production. Assuming natural gas based DRI is then converted to hydrogen, we would expect a further 20-40% reduction in greenhouse gas emissions. While this technology is generally known, it is not commercially available yet.
Carbon Capture, Use, and/or Storage
The introduction of Carbon Capture, Use, and/or Storage into our operations can lead to decreased emissions. We expect that operational blast furnaces will eventually need to have some sort of carbon capture technology employed to continue operating by mid-century. Carbon capture currently exists in the power industry, however there is limited experience in the steel industry, and we do not expect it to be fully commercialized for at least another decade, although there are a number of potential vendors developing the technology. This includes the potential of capturing carbon dioxide from our integrated operations (e.g., coke plants, blast furnaces, oxygen steelmaking furnaces) as well as exploring the potential to capture carbon from our EAF-based operations. The amount of reduction depends on the deployment and the future asset base and potential reductions are not estimable at this time.
Electric grid improvements
Electric grid improvements are needed to allow U. S. Steel to obtain reliable, low-cost, carbon-free power at all our operating locations. While we do procure some carbon-free power currently, we consider this accelerating after 2030 due to several factors including:
- Increased deployment of carbon-free energy sources such as nuclear, hydro, solar, and wind power,
- Increased ability of the grid to transport electricity from where it is generated to where it is needed, and
- The growth of short- and medium-term battery storage, to enable carbon-free power when renewables or other carbon-free options are not available.
Expansion of electrification and hydrogen use
Throughout our processes, we use carbon-containing fuels such as natural gas, diesel, fuel oil, and/or gasoline for process heating, building heating, and transportation. We believe we will be able to reduce our use of these carbon-containing fuels by increasing our use of hydrogen and/or electricity, reducing GHG emissions. This includes using hydrogen or electricity to replace natural gas in hot strip mill reheat furnaces and annealing furnaces, as well as examining the potential for the use of either of these to power light-, medium- and heavy-duty mobile equipment.
Carbon offsets/credits
To achieve net-zero emissions by 2050, we anticipate any gaps remaining from the above processes can potentially be closed through the use of carbon offsets or credits. Offsets and credits are a last resort, and our preference would be to lower emissions as much as possible through technological means before purchasing offsets and credits.
We know achieving our specific goal of net-zero GHG emissions by 2050 and the global goal of limiting global warming to 1.5C requires extraordinary action from every company, industry, sector, and government. We expect to do our part by partnering to find new business approaches and develop new technologies, as well as advocating for collaboration and support of governments, trade agencies, and other organizations. This includes our previously announced Memorandum of Understanding with Equinor to jointly study the potential for carbon capture and storage and hydrogen development in the Ohio, Pennsylvania, and West Virginia region, as well as the recently announced alliance facilitated by IN-2-Market focusing on establishing a regional low-carbon and hydrogen industrial hub in the Northern Appalachian Region. We are working with various universities and the United States Department of Energy on a number of different projects to reduce energy and increase efficiency in our operations.
Greenhouse Gas (GHG): A gas, such as carbon dioxide or methane, that absorbs and emits radiant energy within the thermal infrared range, which causes the greenhouse effect.
Carbon Dioxide equivalents (CO2e): CO2e is a term for normalizing the greenhouse gas effect of different greenhouse gases into a common unit.
Net-Zero: A target for completely negating the amount of greenhouse gases produced by human activity.
Carbon offsets: A reduction or removal of greenhouse gases from the atmosphere to compensate for emissions made internally.
Direct Reduced Iron (DRI): DRI is the product of the direct reduction of iron ore in the solid state by carbon monoxide and hydrogen derived from natural gas or coal.
Hot Briquetted Iron (HBI): HBI is DRI that is subsequently compacted into a briquette while the DRI is still hot. It is used as a supplement for pig iron and scrap in the electric furnace steel mills.
Electric Arc Furnace (EAF): An EAF is a furnace that heats solid steel scrap and other iron units by using an electric arc.
Basic Oxygen Furnace (BOF): A BOF is a furnace that converts liquid iron and steel scrap into liquid steel.
Mini mill Steelmaking: A generalized term referring to operations that consist of an EAF to melt steel scrap and compact continuous casting technology.
Integrated Steelmaking: A process for making steel that uses a blast furnace to produce liquid iron, then converts that liquid iron to liquid steel in a BOF.
Carbon Capture, Use, and/or Storage (CCUS): CCUS is the process of capturing carbon dioxide before it enters the atmosphere, transporting it, and storing or using it as a precursor chemical for other materials.
Green Hydrogen: Green hydrogen is hydrogen produced by splitting water into hydrogen and oxygen using renewable energy.
Blue Hydrogen: Blue hydrogen is hydrogen produced from natural gas, where any GHG emissions from the process are captured and either stored or used in another process.
Scope 1: direct emissions from owned or controlled sources
Scope 2: indirect emissions from the generation of purchased electricity, steam, heating and cooling consumed by a company
Carbon Dioxide equivalents (CO2e): CO2e is a term for normalizing the greenhouse gas effect of different greenhouse gases into a common unit.
Net-Zero: A target for completely negating the amount of greenhouse gases produced by human activity.
Carbon offsets: A reduction or removal of greenhouse gases from the atmosphere to compensate for emissions made internally.
Direct Reduced Iron (DRI): DRI is the product of the direct reduction of iron ore in the solid state by carbon monoxide and hydrogen derived from natural gas or coal.
Hot Briquetted Iron (HBI): HBI is DRI that is subsequently compacted into a briquette while the DRI is still hot. It is used as a supplement for pig iron and scrap in the electric furnace steel mills.
Electric Arc Furnace (EAF): An EAF is a furnace that heats solid steel scrap and other iron units by using an electric arc.
Basic Oxygen Furnace (BOF): A BOF is a furnace that converts liquid iron and steel scrap into liquid steel.
Mini mill Steelmaking: A generalized term referring to operations that consist of an EAF to melt steel scrap and compact continuous casting technology.
Integrated Steelmaking: A process for making steel that uses a blast furnace to produce liquid iron, then converts that liquid iron to liquid steel in a BOF.
Carbon Capture, Use, and/or Storage (CCUS): CCUS is the process of capturing carbon dioxide before it enters the atmosphere, transporting it, and storing or using it as a precursor chemical for other materials.
Green Hydrogen: Green hydrogen is hydrogen produced by splitting water into hydrogen and oxygen using renewable energy.
Blue Hydrogen: Blue hydrogen is hydrogen produced from natural gas, where any GHG emissions from the process are captured and either stored or used in another process.
Scope 1: direct emissions from owned or controlled sources
Scope 2: indirect emissions from the generation of purchased electricity, steam, heating and cooling consumed by a company
Net-Zero Reduction Roadmap Disclaimer
This webpage contains information that may constitute “forward-looking statements” within the meaning of Section 27A of the Securities Act of 1933, as amended, and Section 21E of the Securities Exchange Act of 1934, as amended. We intend the forward-looking statements to be covered by the safe harbor provisions for forward-looking statements in those sections. Generally, we have identified such forward-looking statements by using the words “believe,” “expect,” “intend,” “estimate,” “anticipate,” “project,” “target,” “forecast,” “aim,” “should,” “will,” "may" and similar expressions or by using future dates in connection with any discussion of, among other things, statements about our future business operations, our new product offerings, our market risk, the construction or operation of new or existing facilities, improvement or availability of existing and developing technologies, and our risk management, including climate-related risks and opportunities. However, the absence of these words or similar expressions does not mean that a statement is not forward-looking. Forward-looking statements are not historical facts, but instead represent only the Company’s beliefs regarding future events, many of which, by their nature, are inherently uncertain and outside of the Company’s control. It is possible that the Company’s actual results may differ, possibly materially, from the anticipated results indicated in these forward-looking statements. Management believes that these forward-looking statements are reasonable as of the time made. However, caution should be taken not to place undue reliance on any such forward-looking statements because such statements speak only as of the date when made. Our Company undertakes no obligation to publicly update or revise any forward-looking statements, whether as a result of new information, future events or otherwise, except as required by law. In addition, forward-looking statements are subject to certain risks and uncertainties that could cause actual results to differ materially from our Company's historical experience and our present expectations or projections. These risks and uncertainties include, but are not limited to, the risks and uncertainties described on this webpage and in “Item 1A. Risk Factors” in our Annual Report on Form 10-K and those described from time to time in our reports filed with the Securities and Exchange Commission.
References to "we," "us," "our," the "Company," and "U. S. Steel," refer to United States Steel Corporation and its consolidated subsidiaries and references to “Big River Steel” refer to Big River Steel Holdings LLC and its direct and indirect subsidiaries unless otherwise indicated by the context.
The inclusion of information on this webpage should not be construed as a characterization regarding the materiality or financial impact (or potential impact) of that information. For additional information regarding U. S. Steel, please see our current and periodic reports filed with the Securities and Exchange Commission, including our Annual Report on Form 10-K and Quarterly Reports on Form 10-Q.